From the moment I learned someone was working on a documentary on the Ho 229 I was hooked. This is one of my all time favorite planes, and I've come to learn I'm far from alone in that.
Some of the details of the documentary are still confidential, but suffice it to say that a cockpit mockup was sorely needed and I volunteered to do it. It is to be used as a prop, but the details of how it is to be filmed are still a bit uncertain.
A little background... Here are a few pics of my 1/8 scale model of the Ho 229 and the cockpit I made for it. This is a flying R/C (radio controlled) model that uses electric ducted fans for power. More on this model at http://www.wingsontheweb.com/ho229/ if anyone is interested.


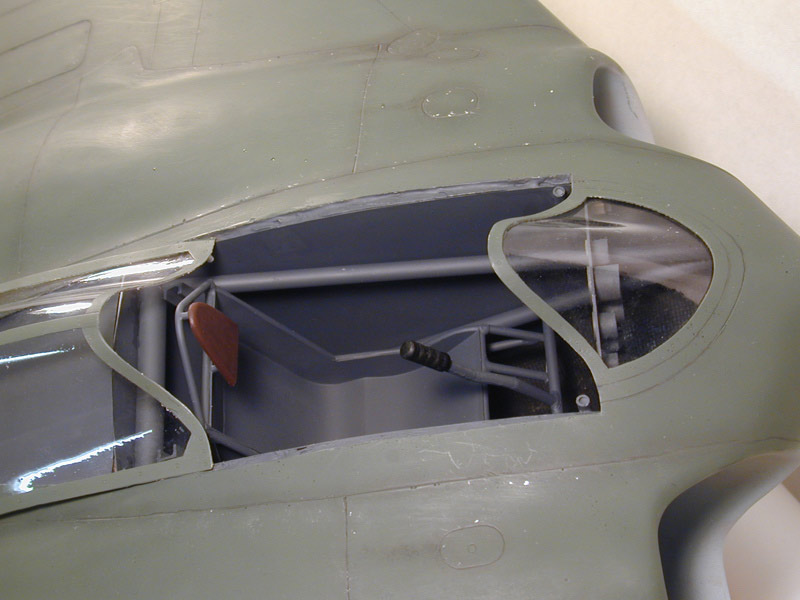

So the basic idea is to make a more detailed version of this cockpit, only 8 times the size! I'm going to try to make it as realistic looking as possible.
Here are a few shots of the CAD workspace. Not quite sure how this will look munged down to 80K. Should give you an idea though.
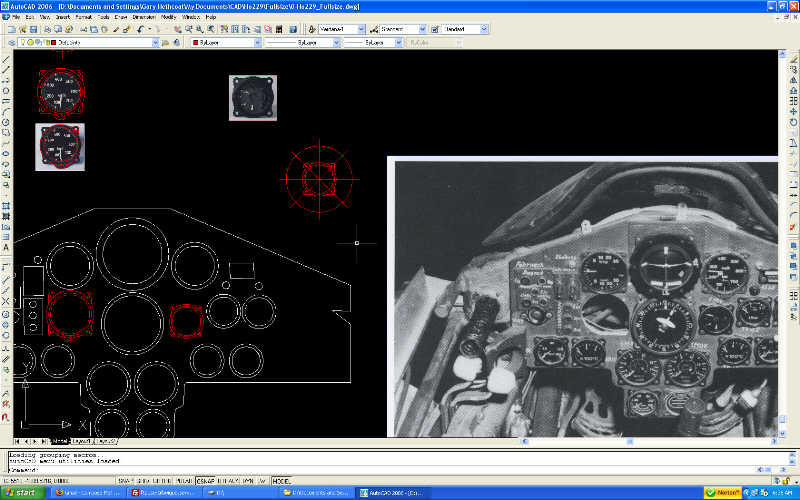

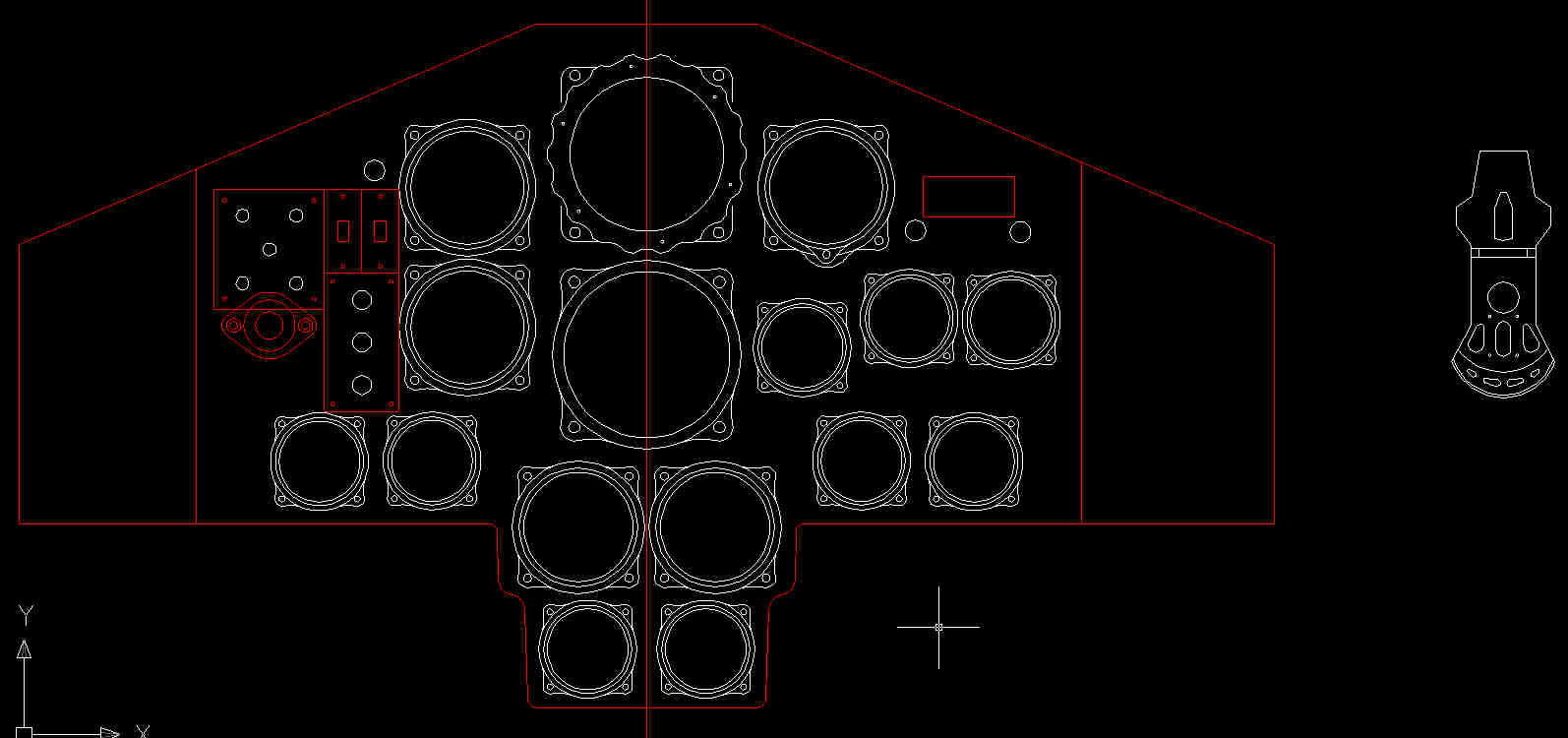
My current plan is as follows. Tubular framework made out of ABS and PVC pipe as used for plumbing. Instrument panel & bezels laser cut from ply. Instrument faces will be photo reproductions with acrylic over top.
The seat will be made per the original, welded steel tubing! This is going to be the challenging part since I've never done any welding before. The problem is, I *know* people are going to want to sit in it, and no other material would be strong enough to take the abuse. The stick and other details will be either plywood, PVC or more steel tubing depending on how the welding goes.
I've got my hands on an acetylene welding/cutting outfit. A bit scary but also exciting!!! Ever seen the Beevis & Butthead show where Beevis goes around saying "Fire. Fire." when he's playing with matches? :-) Just have to figure out how to get the job done without burning myself or the house down :-)
Gary
[Work began on this project at the beginning of October, 2008. I created this blog on Sat Oct 25 and copied the content from the original blog on RCSCALEBUILDER.com]